5 reasons why analysing barrier failures is better than 5-why
I hope you'll forgive me, but I don't really like 5-why. It's a decent methodology, but I think there are better options. Instead, we can use barrier-based incident analysis methods. Why is this better? Well, here are 5 reasons why I think analysing barrier failures is better than 5-why.
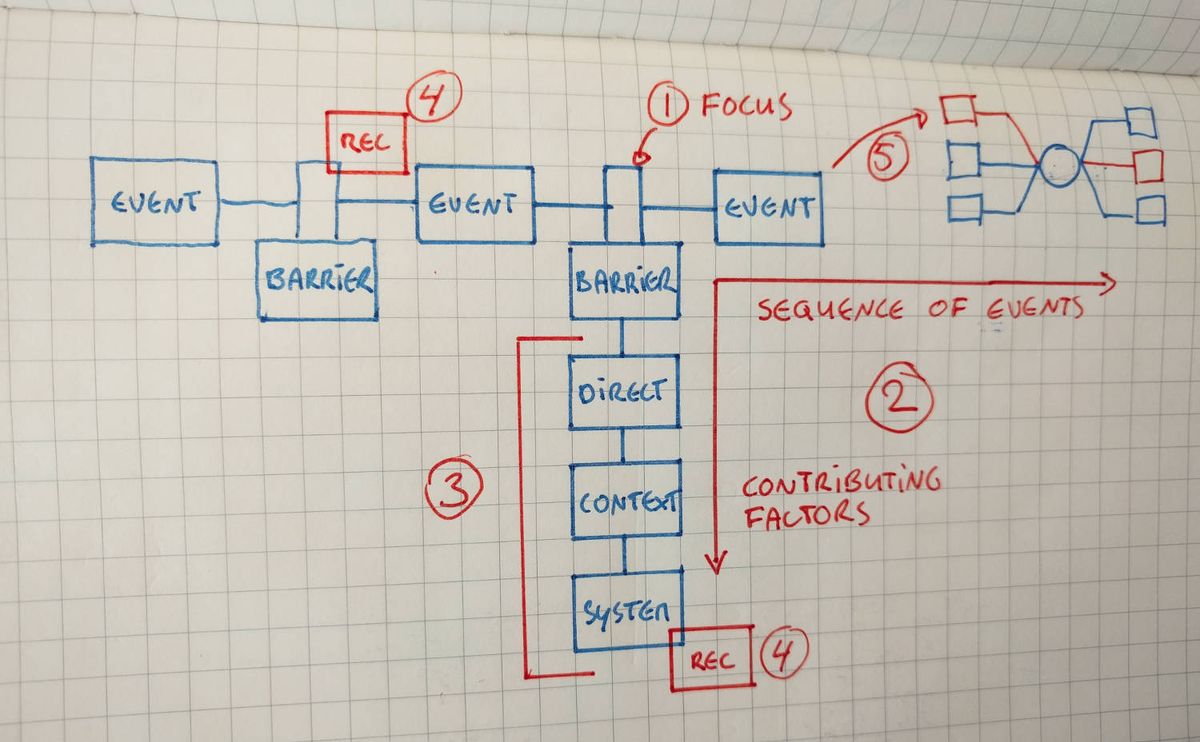
I hope you'll forgive me, but I don't really like 5-why. It's a decent methodology (especially if you don't do incident analysis often), but in my opinion there are better options. Instead, we can use barrier-based incident analysis methods like Tripod Beta, Barrier Failure Analysis or BSCAT. I'll use Barrier Failure Analysis (BFA) to explain. If you don't know what BFA is, take a look at the picture in this post. Why is this better? Well, here are 5 reasons why I think analysing barrier failures is better than 5-why.
1. Barriers focus your attention
In a 5-why diagram, everything is an event or a root cause. If the incident is large, this can lead to an overwhelming amount of information with no difference between important and supporting events. In barrier failure analysis, events are scaffolding that allow us to identify barriers. Barriers are what the organisation should have had in place and it is where our focus should be. During the investigation this focus is useful to spend the resources we have in the right place. After the investigation is complete, this focus is also useful to communicate more effectively to people that weren't part of the investigation team.
2. There is a clear visual sequence of events
A 5-why diagram flows in one direction. Both the sequence of events and the contributing factors are all displayed from, for instance, left to right. Barrier failure diagrams flow in two directions. The events and barriers are modeled horizontally, and the barrier failure causations are vertical. This makes it easier to distinguish between the direct sequence of events in the incident and the underlying contributing factors.
This is not unique to barrier failure diagrams. For instance causal factors charting [1] also flows in two directions.
3. It's more difficult to stop the analysis too early
5-why gives little guidance beyond asking why and ending up with a root cause. This can lead to root causes which aren't useful root causes. The analysis can stop too early (e.g. 'warning signs were absent', without diving into why they were absent) or actually go too far (everything was 'poor safety culture'). In barrier failure analysis, this problem is reduced by giving each level in the causation path a specific purpose. You describe the immediate cause first, then the context in which that immediate cause can happen, and finally the underlying system level cause. In 5-why, the 5 levels don't have a meaning (except for the final one), which makes it more difficult for people to guide their analysis in the right direction.
4. Recommendations can focus on immediate and long term interventions
There are two logical places in a barrier failure analysis where recommendations can be made. On the barrier for more immediate corrective actions, and on the underlying cause for a more long term systematic intervention. Both are useful because we can first get up and running safely in the short term, and then prevent recurrence in the long term. The recommendations in 5-why usually focus more exclusively on root causes, and thus on the long term only.
5. It's easier to connect to existing risk assessments
Any risk assessment method you use already has the concept of barriers (control measures, IPL's, safeguards or something similar). It's weird to have different ways of thinking for incident analysis and risk assessment when they are really two sides of the same coin. With a barrier-based incident analysis method you can more easily connect back to the barriers in an existing risk assessment. This can be useful for trending across incidents and to add new incident scenarios to the risk assessments.
If you want to know more about barrier failure analysis, we have a great course on incident analysis with barriers on 5-6 June in Leidschendam, The Netherlands. Go to slicerisk.com or view the brochure